Jak poradzić sobie z rosnącymi kosztami energetycznymi w przemyśle
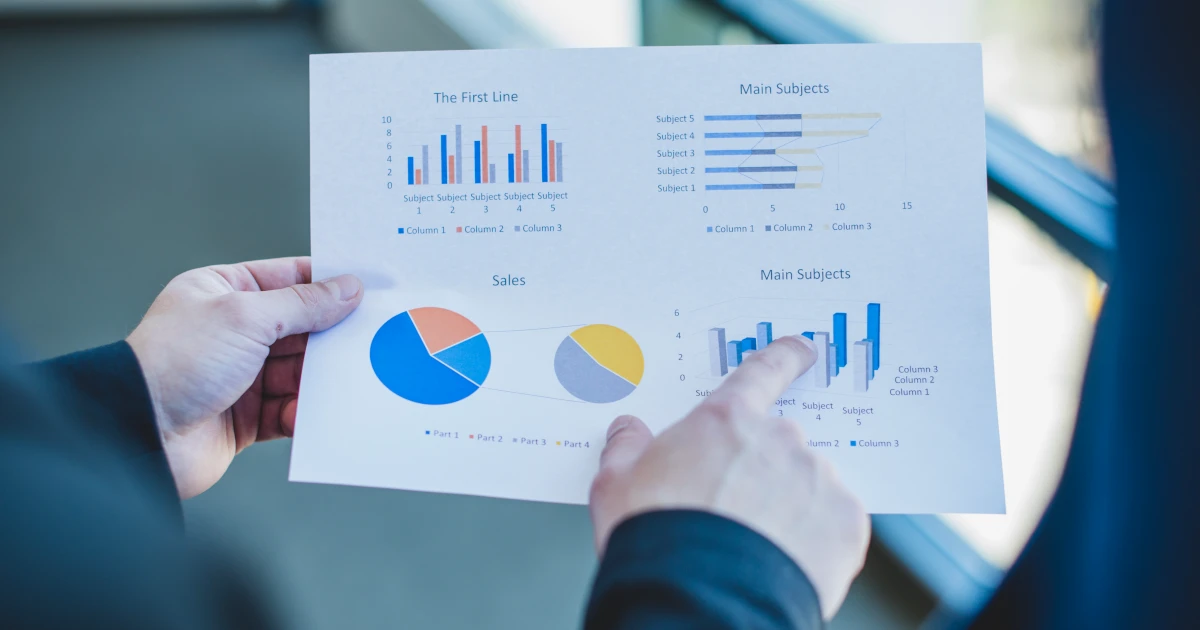
W ostatnich latach obserwujemy niepokojący trend wzrostu cen energii elektrycznej w Polsce. Ten gwałtowny skok stawek za prąd stanowi poważne wyzwanie dla rodzimego przemysłu, który musi stawić czoła rosnącym kosztom produkcji. Niestabilna sytuacja na rynku energetycznym, zależność od importowanych surowców i konieczność transformacji w kierunku źródeł odnawialnych to tylko niektóre czynniki napędzające tę niekorzystną tendencję.
Skutki wzrostu cen prądu dla polskich przedsiębiorstw produkcyjnych są daleko idące. Wyższe rachunki za energię elektryczną bezpośrednio przekładają się na zwiększone wydatki operacyjne, a co za tym idzie – obniżenie rentowności i konkurencyjności. Firmy stoją przed dylematem – przerzucić podwyżki na konsumentów poprzez podniesienie cen produktów, czy znaleźć inne sposoby na pokrycie rosnących kosztów energetycznych.
Ponadto, rosnące ceny prądu mogą zniechęcać potencjalnych inwestorów do lokowania kapitału w polskim przemyśle, co w dłuższej perspektywie może negatywnie wpłynąć na rozwój gospodarczy kraju. Dlatego tak istotne jest wypracowanie skutecznych strategii radzenia sobie z tym wyzwaniem.
Skutki wzrostu cen prądu dla polskiego przemysłu
Wzrost cen energii elektrycznej ma daleko idące konsekwencje dla polskiego sektora przemysłowego. Przedsiębiorstwa produkcyjne, które tradycyjnie były siłą napędową gospodarki, znalazły się w niezwykle trudnej sytuacji.
Po pierwsze, wyższe rachunki za prąd bezpośrednio uderzają w rentowność firm. W wielu gałęziach przemysłu, gdzie koszty energii stanowią znaczącą część budżetu operacyjnego, gwałtowne podwyżki mogą prowadzić do erozji zysków lub wręcz strat. To z kolei może zmusić przedsiębiorstwa do cięcia innych wydatków, takich jak inwestycje w rozwój lub wynagrodzenia pracowników.
Po drugie, rosnące koszty energii elektrycznej wpływają na konkurencyjność polskich produktów na rynkach krajowych i zagranicznych. Jeśli firmy zdecydują się przerzucić podwyżki na konsumentów, ich towary staną się droższe w porównaniu z ofertą konkurencji z krajów o niższych cenach prądu. To może prowadzić do utraty udziałów rynkowych i spadku sprzedaży.
Ponadto, wysokie koszty energii mogą zniechęcać inwestorów do lokowania kapitału w polskim przemyśle. Nowe inwestycje są kluczowe dla rozwoju i modernizacji sektora produkcyjnego, a niepewność co do przyszłych cen prądu może skutecznie je ograniczyć.
Analiza kosztów produkcji w związku ze wzrostem cen prądu
Aby skutecznie poradzić sobie z wyzwaniem rosnących cen energii elektrycznej, kluczowe jest dokładne zrozumienie struktury kosztów produkcji w przedsiębiorstwie. Tylko w ten sposób można opracować odpowiednie strategie oszczędzania i optymalizacji zużycia prądu.
W pierwszym kroku należy przeprowadzić szczegółową analizę, jaką część całkowitych kosztów operacyjnych stanowią wydatki na energię elektryczną. Odsetek ten może znacząco różnić się w zależności od branży i specyfiki produkcji. Przykładowo, w energochłonnych gałęziach, takich jak hutnictwo czy przemysł chemiczny, koszty prądu mogą sięgać nawet 30-40% budżetu operacyjnego.
Następnie warto przyjrzeć się poszczególnym etapom procesu produkcyjnego i zidentyfikować obszary o największym zapotrzebowaniu na energię. Może to być np. obsługa maszyn i urządzeń, oświetlenie hal produkcyjnych czy ogrzewanie/chłodzenie pomieszczeń. Takie mapowanie zużycia prądu pozwoli na opracowanie ukierunkowanych działań oszczędnościowych.
Ważnym elementem analizy jest również ocena możliwości optymalizacji procesów pod kątem efektywności energetycznej. Często proste zmiany, takie jak modernizacja przestarzałych maszyn czy lepsze zarządzanie cyklem produkcyjnym, mogą przynieść znaczące oszczędności energii.
Strategie pokrycia kosztów energetycznych w produkcji taśmowej
Produkcja taśmowa, charakterystyczna dla wielu gałęzi przemysłu, stawia przed firmami szczególne wyzwania w zakresie pokrycia rosnących kosztów energii elektrycznej. Z jednej strony, ciągłość procesu produkcyjnego jest kluczowa dla zapewnienia odpowiedniej wydajności i terminowości dostaw. Z drugiej jednak, zużycie prądu na dużą skalę generuje wysokie rachunki, które mogą negatywnie wpłynąć na rentowność.
Jedną ze strategii radzenia sobie z tym problemem jest inwestycja w nowoczesne, energooszczędne maszyny i urządzenia. Choć wiąże się to z początkowymi nakładami finansowymi, w dłuższej perspektywie pozwala na znaczące obniżenie zużycia energii, a co za tym idzie – kosztów operacyjnych. Warto również rozważyć modernizację istniejącego parku maszynowego, np. poprzez wymianę nieefektywnych silników czy instalację systemów odzysku ciepła.
Alternatywnym podejściem jest optymalizacja harmonogramów produkcyjnych w taki sposób, aby zmaksymalizować wykorzystanie maszyn w godzinach, gdy ceny prądu są niższe. Wymaga to ścisłej współpracy z dostawcami energii i dokładnej analizy taryf, ale może przynieść wymierne oszczędności.
Innym rozwiązaniem wartym rozważenia jest inwestycja w systemy zarządzania energią (EMS). Nowoczesne oprogramowanie pozwala na monitorowanie zużycia prądu w czasie rzeczywistym i automatyczną optymalizację procesów pod kątem efektywności energetycznej. Choć wdrożenie EMS wiąże się z dodatkowymi kosztami, w dłuższej perspektywie może znacząco obniżyć rachunki za prąd.
Wykorzystanie maszyn w produkcji i koszty energetyczne
W wielu gałęziach przemysłu produkcja opiera się w dużej mierze na wykorzystaniu maszyn i urządzeń. Ich obsługa i eksploatacja generują znaczące koszty energetyczne, które rosną wraz ze wzrostem cen prądu. Dlatego tak ważne jest wdrożenie skutecznych strategii optymalizacji zużycia energii w tym obszarze.
Jednym z kluczowych działań jest regularna konserwacja i modernizacja parku maszynowego. Przestarzałe urządzenia często charakteryzują się niską efektywnością energetyczną, co prowadzi do nadmiernego zużycia prądu. Inwestycja w nowoczesne, energooszczędne maszyny może znacząco obniżyć rachunki za energię elektryczną.
Innym rozwiązaniem jest wdrożenie systemów monitorowania i zarządzania zużyciem energii przez maszyny. Nowoczesne oprogramowanie pozwala na śledzenie w czasie rzeczywistym, ile prądu zużywają poszczególne urządzenia, i automatyczną optymalizację ich pracy pod kątem efektywności energetycznej.
Warto również rozważyć możliwość wdrożenia technologii odzysku energii, takich jak systemy rekuperacji ciepła. Umożliwiają one wykorzystanie energii odpadowej z procesów produkcyjnych do ogrzewania pomieszczeń lub podgrzewania wody, co może znacząco obniżyć całkowite zużycie prądu.
Oszczędzanie energii w przemyśle - najlepsze praktyki
Wzrost cen energii elektrycznej stanowi poważne wyzwanie dla polskiego przemysłu, ale istnieje wiele sprawdzonych sposobów na obniżenie zużycia prądu i ograniczenie kosztów. Oto niektóre z najlepszych praktyk oszczędzania energii w sektorze produkcyjnym:
-
Audyt energetyczny
- Przeprowadzenie szczegółowego audytu zużycia energii w całym przedsiębiorstwie pozwala zidentyfikować obszary o największym potencjale oszczędnościowym.
- Na podstawie wyników audytu można opracować kompleksowy plan działań optymalizacyjnych.
-
Modernizacja oświetlenia
- Wymiana przestarzałych źródeł światła na energooszczędne LED-y może przynieść znaczące oszczędności.
- Warto również rozważyć instalację systemów sterowania oświetleniem, np. czujników ruchu.
-
Efektywne zarządzanie energią
- Wdrożenie systemów monitorowania i zarządzania zużyciem energii (EMS) umożliwia optymalizację procesów produkcyjnych pod kątem efektywności energetycznej.
- EMS pozwalają również na identyfikację i eliminację marnotrawstwa energii.
-
Odzysk ciepła
- Instalacja systemów rekuperacji ciepła odpadowego z procesów produkcyjnych może znacząco obniżyć zapotrzebowanie na energię do ogrzewania pomieszczeń i wody.
-
Edukacja pracowników
- Podnoszenie świadomości ekologicznej i energetycznej wśród pracowników, np. poprzez szkolenia i kampanie informacyjne, może przyczynić się do zmniejszenia marnotrawstwa energii.
-
Harmonogramowanie produkcji
- Optymalizacja harmonogramów produkcyjnych pod kątem wykorzystania maszyn w godzinach, gdy ceny prądu są niższe, może przynieść wymierne oszczędności.
Wdrożenie tych najlepszych praktyk wymaga często nakładów inwestycyjnych, ale w dłuższej perspektywie przynosi wymierne korzyści w postaci obniżonych kosztów energii elektrycznej i zwiększonej konkurencyjności przedsiębiorstwa.
Alternatywne źródła energii w polskim przemyśle
Rosnące ceny energii elektrycznej z konwencjonalnych źródeł skłaniają polski przemysł do poszukiwania alternatywnych rozwiązań energetycznych. Wykorzystanie odnawialnych źródeł energii (OZE), takich jak energia słoneczna, wiatrowa czy biomasa, może nie tylko obniżyć koszty, ale również wpisać się w trend zrównoważonego rozwoju i ochrony środowiska.
Jedną z opcji wartych rozważenia jest instalacja farm fotowoltaicznych na terenach zakładów produkcyjnych. Choć wiąże się to z początkowymi nakładami inwestycyjnymi, w dłuższej perspektywie może przynieść znaczące oszczędności na rachunkach za prąd. Ponadto, przedsiębiorstwa mogą skorzystać z programów dotacyjnych i ulg podatkowych wspierających inwestycje w OZE.
Innym rozwiązaniem jest wykorzystanie energii wiatrowej poprzez budowę własnych turbin wiatrowych lub nabycie udziałów w istniejących farmach wiatrowych. Ta technologia cieszy się rosnącą popularnością ze względu na relatywnie niskie koszty eksploatacji i coraz większą efektywność.
Alternatywą dla tradycyjnych źródeł energii może być również biomasa, np. w postaci odpadów drzewnych lub rolniczych. Spalanie biomasy w specjalnych kotłach pozwala na produkcję ciepła i energii elektrycznej, a przy tym charakteryzuje się niską emisją CO2.
Warto jednak pamiętać, że wybór odpowiedniego źródła OZE powinien być poprzedzony dokładną analizą warunków lokalnych, takich jak nasłonecznienie, warunki wietrzne czy dostępność biomasy. Tylko w ten sposób można maksymalnie wykorzystać potencjał alternatywnych źródeł energii.
Cięcie kosztów energetycznych - skuteczne metody
W obliczu rosnących cen prądu, polskie przedsiębiorstwa produkcyjne stoją przed wyzwaniem znalezienia skutecznych metod cięcia kosztów energetycznych. Oto kilka sprawdzonych rozwiązań, które warto wziąć pod uwagę:
-
Audyt energetyczny i plan oszczędnościowy
- Przeprowadzenie szczegółowego audytu zużycia energii w firmie pozwala zidentyfikować obszary marnotrawstwa i największe źródła kosztów.
- Na podstawie wyników audytu można opracować kompleksowy plan działań oszczędnościowych, obejmujący m.in. modernizację infrastruktury, optymalizację procesów produkcyjnych i wdrożenie systemów zarządzania energią.
-
Negocjacje z dostawcami energii
- Regularne negocjacje warunków umów z dostawcami energii elektrycznej mogą przynieść korzystne stawki i obniżyć rachunki za prąd.
- Warto rozważyć zmianę dostawcy lub przejście na taryfy uwzględniające zróżnicowanie cen w zależności od pory dnia i obciążenia sieci.
-
Inwestycje w efektywność energetyczną
- Modernizacja przestarzałych maszyn i urządzeń na energooszczędne może znacząco obniżyć zużycie energii.
- Instalacja systemów odzysku ciepła, oświetlenia LED czy automatyki sterującej zużyciem prądu to kolejne skuteczne rozwiązania.
-
Optymalizacja procesów produkcyjnych
- Przeprojektowanie procesów pod kątem minimalizacji zużycia energii, np. poprzez harmonogramowanie produkcji w godzinach niższych staw ek, może przynieść znaczące oszczędności.
-
Wykorzystanie odnawialnych źródeł energii
- Inwestycja w instalacje fotowoltaiczne, turbiny wiatrowe czy systemy wykorzystujące biomasę pozwala na produkcję energii ze źródeł odnawialnych i uniezależnienie się od wahań cen prądu z sieci.
- Przedsiębiorstwa mogą skorzystać z licznych programów dotacyjnych i ulg podatkowych wspierających inwestycje w odnawialne źródła energii.
-
Edukacja i zaangażowanie pracowników
- Podnoszenie świadomości ekologicznej i energetycznej wśród załogi, np. poprzez szkolenia i kampanie informacyjne, może przyczynić się do zmniejszenia marnotrawstwa energii.
- Zachęcanie pracowników do zgłaszania pomysłów na oszczędzanie prądu i wdrażanie najlepszych rozwiązań buduje kulturę efektywności energetycznej w firmie.
Wdrożenie tych metod cięcia kosztów energetycznych wymaga często nakładów inwestycyjnych, ale w dłuższej perspektywie przynosi wymierne korzyści w postaci obniżonych rachunków za prąd, zwiększonej konkurencyjności i zrównoważonego rozwoju przedsiębiorstwa.
Wzrost cen energii elektrycznej to jedno z największych wyzwań, przed którymi stoi obecnie polski przemysł. Jednak odpowiednie strategie i działania oszczędnościowe pozwalają skutecznie poradzić sobie z tym problemem. Kluczowe jest zrozumienie struktury kosztów energetycznych w przedsiębiorstwie, wdrożenie najlepszych praktyk optymalizacji zużycia prądu oraz rozważenie inwestycji w odnawialne źródła energii. Tylko w ten sposób polskie firmy produkcyjne będą mogły utrzymać konkurencyjność i zapewnić dalszy rozwój w obliczu rosnących cen energii.
ZOBACZ RÓWNIEŻ:
- Jak motywować pracowników do przestrzegania zasad BHP
- Dezynfekcja hal produkcyjnych czyli skuteczność ozonowania w walce z bakteriami i wirusami
- Dlaczego branża przemysłowa potrzebuje nowoczesnej strony internetowej w dzisiejszych czasach
- Wymogi prawne dla hali produkcyjnej: Kompleksowe przewodnik dla branży produkcji
- Jak dobrać trwałe i optymalne opakowanie kartonowe dla części samochodowych podatnych na korozję?