Wszystko, co musisz wiedzieć o technologii CNC
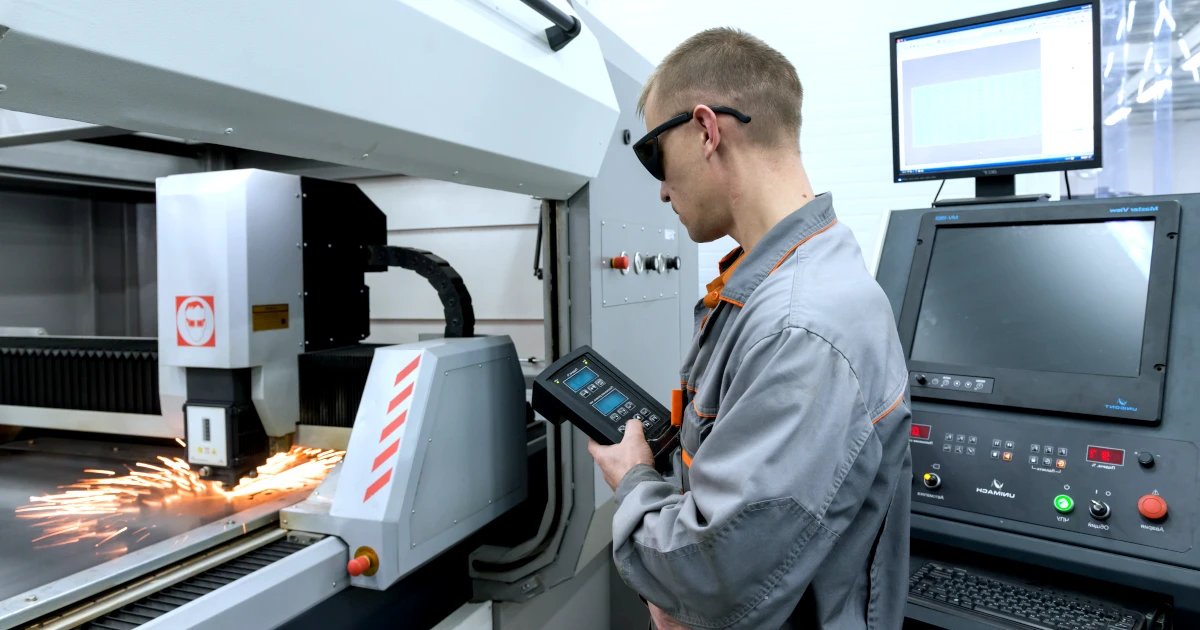
Technologia CNC, czyli Komputerowo Sterowane Obróbki Numerycznej (ang. Computer Numerical Control), to zaawansowany system automatyzacji produkcji, który umożliwia precyzyjną obróbkę różnych materiałów, takich jak metal, drewno czy tworzywa sztuczne. W przeciwieństwie do tradycyjnych metod obróbki ręcznej, technologia CNC wykorzystuje zaprogramowane komputerowo maszyny do wykonywania złożonych kształtów, wzorów i detali z wysoką dokładnością.
Serce systemu CNC to sterownik komputerowy, który na podstawie zaprogramowanych instrukcji precyzyjnie kontroluje ruch narzędzi obróbczych, takich jak frezarki, tokarki czy wiertarki. Dzięki temu możliwe jest wykonywanie zaawansowanych operacji, takich jak cięcie, toczenie, frezowanie, wiercenie czy szlifowanie, z powtarzalną dokładnością i wydajnością. Technologia CNC pozwala na produkcję wysokiej jakości elementów, które znajdują zastosowanie w wielu gałęziach przemysłu, od motoryzacji po lotnictwo.
Kluczową zaletą technologii CNC jest jej wszechstronność. Maszyny CNC mogą być zaprogramowane do wykonywania praktycznie dowolnych kształtów i form, co czyni je niezwykle elastycznymi narzędziami w rękach wykwalifikowanych operatorów. Ponadto, nowoczesne systemy CNC są wyposażone w zaawansowane funkcje, takie jak automatyczna wymiana narzędzi, monitorowanie procesu obróbki czy integracja z systemami CAD/CAM, które jeszcze bardziej zwiększają efektywność i wydajność produkcji.
Zalety technologii CNC w obróbce metalu
Technologia CNC jest szczególnie ceniona w przemyśle metalowym, gdzie umożliwia wykonywanie precyzyjnych, powtarzalnych i złożonych kształtów. Niektóre z kluczowych zalet zastosowania CNC w obróbce metalu to:
-
Wysoka Dokładność i Powtarzalność: Maszyny CNC zapewniają niezwykłą precyzję w wykonywaniu detali, co przekłada się na lepszą jakość produktów końcowych. Dzięki komputerowej kontroli nad ruchem narzędzi, możliwe jest uzyskiwanie powtarzalnych wyników, nawet przy produkcji dużych serii.
-
Zwiększona Wydajność: Zautomatyzowane procesy CNC pozwalają na znaczne skrócenie czasu produkcji, co przekłada się na wyższą wydajność i niższe koszty. Maszyny CNC mogą pracować przez całą dobę, bez konieczności przerw na odpoczynek.
-
Kompleksowa Obróbka: Technologia CNC umożliwia wykonywanie wielu różnorodnych operacji obróbczych, takich jak frezowanie, toczenie, wiercenie czy cięcie, na jednej maszynie. Pozwala to na zintegrowanie procesu produkcyjnego i ograniczenie liczby etapów.
-
Oszczędność Materiałów: Dzięki precyzyjnemu sterowaniu ruchem narzędzi, maszyny CNC generują mniej odpadów w porównaniu do tradycyjnych metod obróbki. Pozwala to na znaczne zmniejszenie kosztów materiałowych.
-
Zwiększona Elastyczność: Programowanie maszyn CNC umożliwia szybkie i łatwe wprowadzanie zmian w projektach, co czyni ten system niezwykle elastycznym. Pozwala to na efektywne dostosowywanie się do zmieniających się wymagań rynku.
Połączenie tych zalet sprawia, że technologia CNC jest coraz częściej wybierana przez przedsiębiorstwa z branży metalowej, które dążą do zwiększenia wydajności, jakości i konkurencyjności swojej produkcji.
Statystyki dotyczące technologii CNC
Technologia CNC zyskuje na popularności na całym świecie, o czym świadczą następujące statystyki:
- Globalny rynek maszyn CNC szacowany jest na ponad 80 miliardów dolarów w 2022 roku i oczekuje się, że do 2027 roku wzrośnie do 100 miliardów dolarów.
- Według badań, 85% firm produkcyjnych w Stanach Zjednoczonych wykorzystuje technologię CNC w swojej działalności.
- W Europie ponad 70% przedsiębiorstw z sektora obróbki metali korzysta z systemów CNC.
- Prognozuje się, że do 2025 roku liczba zainstalowanych maszyn CNC na świecie osiągnie ponad 5 milionów sztuk.
- Wśród kluczowych czynników napędzających wzrost rynku CNC wymienia się m.in. rosnące zapotrzebowanie na precyzyjne i zautomatyzowane procesy produkcyjne oraz rozwój technologii cyfrowych.
Powyższe dane jednoznacznie wskazują, że technologia CNC staje się standardem w nowoczesnym przemyśle, a jej zastosowanie przynosi wymierne korzyści przedsiębiorstwom poszukującym efektywnych i konkurencyjnych rozwiązań produkcyjnych.
Programowanie maszyn CNC
Jednym z kluczowych aspektów technologii CNC jest programowanie maszyn, które umożliwia precyzyjne sterowanie procesem obróbki. Operatorzy CNC muszą posiadać specjalistyczną wiedzę i umiejętności w zakresie tworzenia programów obróbczych, aby w pełni wykorzystać możliwości maszyn.
Proces programowania CNC zazwyczaj składa się z kilku etapów:
-
Projektowanie Modelu CAD: Pierwszy krok to stworzenie projektu 3D detalu lub elementu, który ma zostać wyprodukowany. Wykorzystuje się do tego zaawansowane oprogramowanie CAD (Computer-Aided Design).
-
Konwersja do Formatu CNC: Następnie model CAD jest konwertowany do formatu zrozumiałego dla sterownika maszyny CNC, najczęściej jest to format G-code.
-
Symulacja Procesu Obróbki: Przed uruchomieniem maszyny, program obróbczy jest poddawany symulacji, aby zweryfikować poprawność działania i wykryć ewentualne błędy.
-
Optymalizacja Programu: Na tym etapie program jest optymalizowany pod kątem wydajności, minimalizacji czasu obróbki oraz zużycia narzędzi.
-
Przygotowanie Maszyny: Ostatnim krokiem jest właściwe przygotowanie maszyny CNC do pracy, m.in. poprzez załadowanie programu, ustawienie narzędzi i materiału.
Umiejętne programowanie maszyn CNC jest kluczowe dla uzyskania wysokiej jakości produktów, powtarzalności procesów oraz maksymalnej efektywności produkcji. Dlatego też operatorzy CNC muszą stale doskonalić swoje kompetencje, aby sprostać rosnącym wymaganiom rynku.
Tworzenie projektów i modeli do obróbki CNC
Projektowanie i modelowanie 3D odgrywają kluczową rolę w technologii CNC. Zaawansowane oprogramowanie CAD umożliwia tworzenie precyzyjnych modeli cyfrowych, które następnie mogą być wykorzystywane do generowania programów obróbczych.
Proces tworzenia projektów i modeli do obróbki CNC obejmuje następujące etapy:
-
Analiza Wymagań: Na początku należy dokładnie określić parametry i specyfikacje detalu, który ma zostać wyprodukowany.
-
Projektowanie w CAD: Przy użyciu oprogramowania CAD, takich jak AutoCAD, SolidWorks czy Fusion 360, projektant tworzy cyfrowy model 3D przyszłego produktu.
-
Optymalizacja Modelu: Model jest poddawany analizie i optymalizacji pod kątem obrabialności, minimalizacji odpadów oraz ograniczeń wynikających z technologii CNC.
-
Generowanie Programu Obróbczego: Następnie model 3D jest konwertowany do formatu zrozumiałego przez sterownik maszyny CNC, najczęściej G-code, który definiuje ścieżki narzędzi i parametry obróbki.
-
Symulacja i Weryfikacja: Przed uruchomieniem maszyny, program obróbczy jest poddawany szczegółowej symulacji, aby zweryfikować jego poprawność i wykryć ewentualne błędy.
Umiejętne tworzenie projektów i modeli 3D jest kluczowe dla powodzenia procesu produkcji CNC. Pozwala to na uzyskanie wysokiej jakości produktów, skrócenie czasu obróbki oraz minimalizację kosztów.
Techniki cięcia, skrawania, przycinania i gięcia w technologii CNC
Technologia CNC oferuje szereg zaawansowanych technik obróbczych, które umożliwiają precyzyjne kształtowanie różnorodnych materiałów. Wśród najczęściej stosowanych procesów można wymienić:
-
Cięcie CNC: Maszyny CNC wyposażone w narzędzia tnące, takie jak lasery, plazmy czy wodne strumienie, pozwalają na precyzyjne cięcie blach, rur, profili oraz innych elementów metalowych.
-
Skrawanie CNC: Frezarki CNC umożliwiają skrawanie, czyli usuwanie materiału z obrabianego przedmiotu, w celu uzyskania pożądanego kształtu i wykończenia powierzchni.
-
Przycinanie CNC: Tokarki CNC znajdują zastosowanie w precyzyjnym przycinaniu i obróbce obwodowej elementów cylindrycznych, takich jak wałki, tuleje czy trzpienie.
-
Gięcie CNC: Prasy krawędziowe sterowane komputerowo pozwalają na precyzyjne gięcie blach i profili metalowych pod kątem, zapewniając powtarzalność kształtu.
Ponadto, w technologii CNC wykorzystuje się również zaawansowane techniki, takie jak:
- Wiercenie CNC - precyzyjne wykonywanie otworów w obrabianym materiale.
- Szlifowanie CNC - uzyskiwanie wysokiej jakości powierzchni poprzez szlifowanie.
- Tłoczenie CNC - kształtowanie materiału poprzez docisk do formy.
Różnorodność technik obróbczych CNC pozwala na kompleksową realizację nawet najbardziej złożonych projektów produkcyjnych, zapewniając wysoką dokładność i powtarzalność.
Wykorzystanie technologii CNC z wodą i laserem
Oprócz tradycyjnych metod obróbki, technologia CNC znajduje zastosowanie w zaawansowanych technikach, takich jak cięcie wodne i laserowe.
Cięcie Wodne CNC: Cięcie wodne CNC wykorzystuje wysokociśnieniowy strumień wody do precyzyjnego wycinania elementów z różnych materiałów, takich jak metal, kamień, szkło czy tworzywa sztuczne. Zaletami tej metody są:
- Brak ciepła i wibracji, co zapobiega deformacjom materiału
- Możliwość cięcia materiałów wrażliwych na wysoką temperaturę
- Brak konieczności stosowania środków smarnych
- Wysoka dokładność i gładkość krawędzi cięcia
Cięcie Laserowe CNC: Technologia cięcia laserowego CNC wykorzystuje skoncentrowany wiązką lasera do precyzyjnego wycinania elementów z metali, tworzyw sztucznych, drewna i innych materiałów. Wśród jej zalet można wymienić:
- Wąska strefa wpływu ciepła, co pozwala na cięcie delikatnych materiałów
- Wysoka powtarzalność i dokładność cięcia
- Możliwość wycinania bardzo złożonych kształtów
- Brak konieczności stosowania narzędzi tnących
Zarówno cięcie wodne, jak i laserowe CNC znajdują szerokie zastosowanie w nowoczesnym przemyśle, umożliwiając realizację zaawansowanych projektów produkcyjnych przy zachowaniu najwyższej jakości.
Nowoczesne rozwiązania w technologii CNC - przyspieszenie produkcji
Technologia CNC nieustannie ewoluuje, dostarczając coraz bardziej zaawansowanych rozwiązań, które pozwalają na przyspieszenie i ulepszenie procesów produkcyjnych. Wśród najnowszych trendów w technologii CNC można wyróżnić:
-
Integracja z Systemami CAD/CAM: Ścisła współpraca między oprogramowaniem do projektowania CAD a systemami CAM (Computer-Aided Manufacturing) umożliwia płynne przejście od modelu 3D do gotowego programu obróbczego, skracając czas przygotowania produkcji.
-
Automatyzacja i Robotyzacja: Wprowadzanie zrobotyzowanych systemów załadunku/rozładunku, a także automatycznej wymiany narzędzi, pozwala na znaczne zwiększenie wydajności i efektywności linii produkcyjnych CNC.
-
Monitorowanie i Analityka Procesów: Nowoczesne maszyny CNC są wyposażone w zaawansowane systemy monitorowania i analizy danych produkcyjnych, umożliwiając optymalizację procesów i przewidywanie potencjalnych problemów.
-
Łączność i Przemysł 4.0: Coraz częściej maszyny CNC są zintegrowane z sieciami przemysłowymi i systemami IT, pozwalając na zdalne monitorowanie, sterowanie oraz integrację z systemami zarządzania przedsiębiorstwem.
-
Druk 3D i Hybrydowe Technologie: Rozwój technologii druku 3D umożliwia łączenie procesów addytywnych z obróbką CNC, tworząc nowe możliwości w zakresie produkcji zaawansowanych elementów.
ZOBACZ RÓWNIEŻ: